The game-changing picking system boosts efficiency improvement by 200%+
Lift
Tugger
Bin Mover
Robot Arm Hybrid
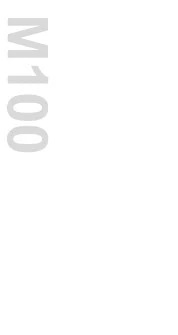
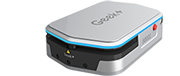
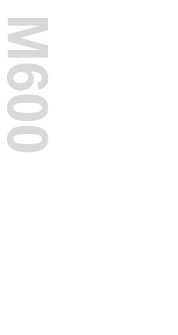
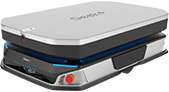
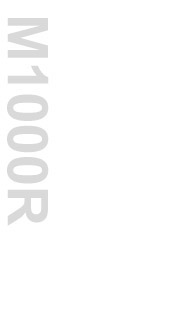
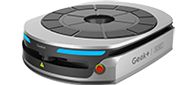
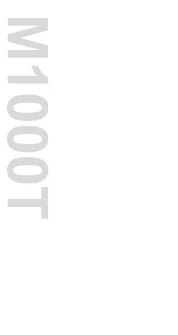
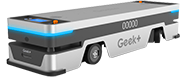
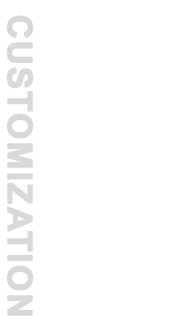
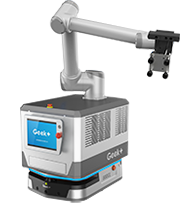
Body dimensions
740*500*210
1080*700*310
1090*830*275
1500*406*300
720*510*660
mm
Rotation diameter
754
1150
1090
1554
754
mm
Maximum load
200~75
600
1000
1000
N/A
kg
Maximum running speed
No-load speed 1.5m/s, full load speed 1.5m/s
No load 1.5m/s, full load 1.5m/s
No-load speed 1.5m/s, full load speed 1.5m/s
No-load speed 1.5m/s, full load speed 1.5m/s
No-load speed 1.5m/s, full load speed 1.5m/s
m/s
Maximum rotation speed
90°/2s,180°/3s
90°/2s,180°/3s
90°/2s,180°/3s
90°/2s,180°/3s
90°/2s,180°/3s
°/s
Control precision
<20mm,2°
<20mm,2°
<20mm,2°
<20mm,2°
<20mm,2°
mm,°
Drive
Two-wheel differential drive
Two-wheel differential drive
Two-wheel differential drive
Two-wheel differential drive
Two-wheel differential drive
–
Navigation method
Laser radar + Reflector
SLAM+assisted navigation+QR code navigation+Vision
SLAM+assisted navigation+QR code navigation+Vision
SLAM+assisted navigation
SLAM+assisted navigation
–
Communication module
WIFI,support 2.4G/5G,IEEE802.11 b/g/n
WIFI,support 2.4G/5G,IEEE802.11 b/g/n
WIFI,support 2.4G/5G,IEEE802.11 b/g/n
WIFI,support 2.4G/5G,IEEE802.11 b/g/n
WIFI,support 2.4G/5G,IEEE802.11 b/g/n
–
Battery
Li-ion battery DC50.4V(typ)24.7Ah
Li-ion battery,DC50.4V(typ),39Ah
Li-ion battery DC50.4V(typ)24.7Ah
Li-ion battery DC50.4V(typ)24.7Ah
Li-ion battery DC50.4V(typ)24.7Ah
V, Ah
Run time
Charging for 10 minutes, working for one hour
Charging for 10 minutes, working for one hour
Charging for 10 minutes, working for one hour
Charging for 10 minutes, working for one hour
Charging for 10 minutes, working for one hour
–
Obstacle detection
270° Laser radar
360° Laser radar
360° Laser radar
360° Laser radar
270° Laser radar
–
Certificate
/
Optional for CE,FCC
CE,FCC
/
/
–
Optional components
Towing,Lifting,Roller, Human-machine interaction platform
Lifting (M600C-END-L)
/
/
Together with cobots, customized grippers and vision system
–
Lift
Geek+ Lift solution includes M1000, M600, M100, and other AMR models equipped with lifting capabilities. The standard lifting module includes SLAM navigation that enables AMRs to follows virtual lines in complex environments. Optional to customize the module for different height, dock mechanisms, and payloads.
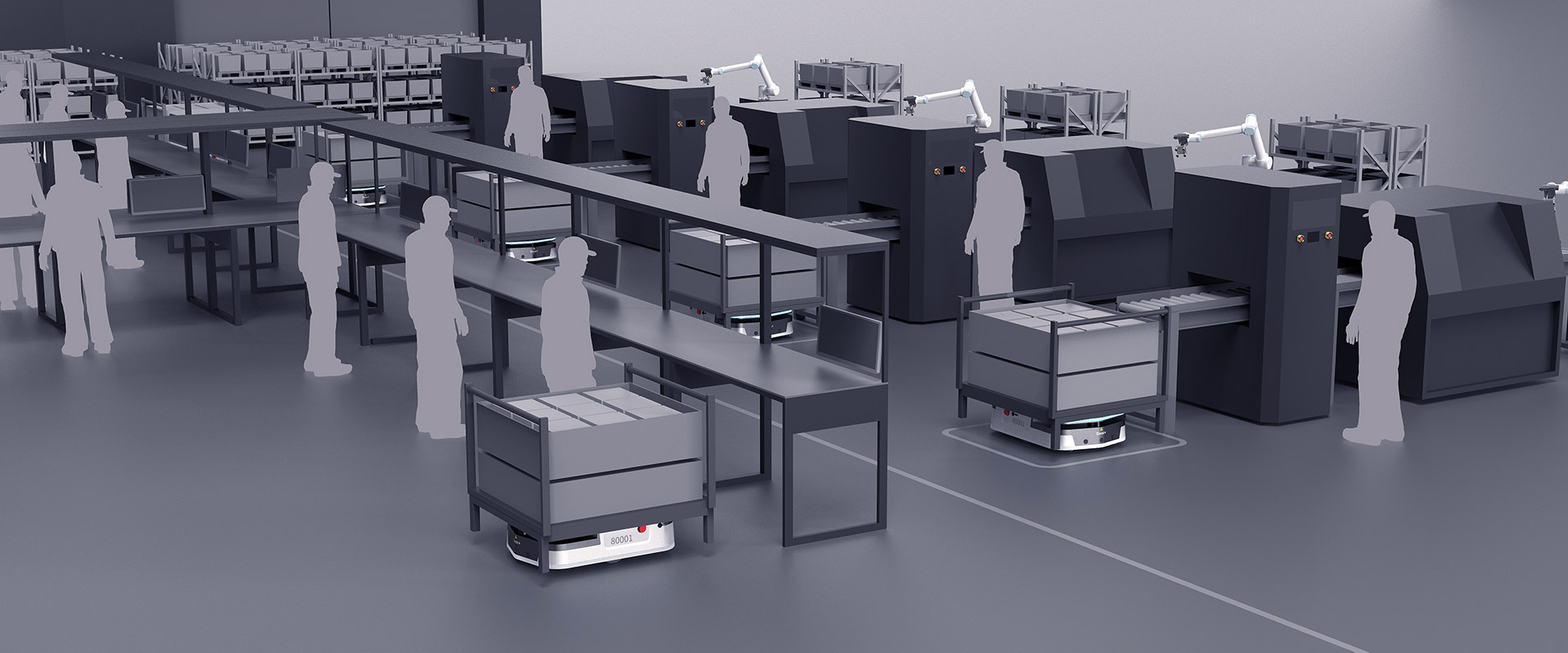
Tugger
Geek+ Tugger solution includes M1000T, M600, M100 and other AMR models equipped with strong pulling capabilities. It can postion carts accurately and handle large carts effectively, also adaptive to different cart sizes. M1000T can tow multiple carts at the same time.
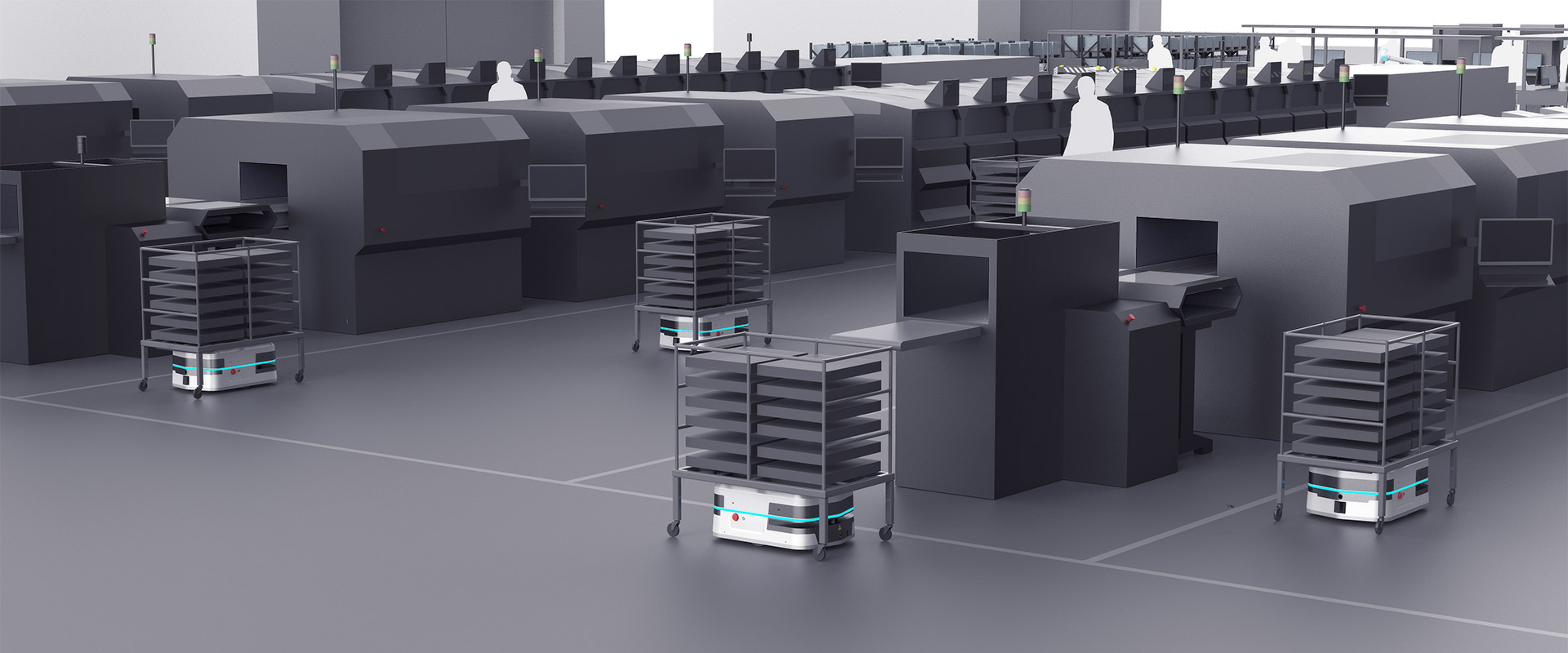
Bin Mover
Geek+ Bin Mover includes M600, M100, and other AMR models equipped with bin moving mechanism. It offers customizable single-box and multi-box operating mechanisms of different sizes, including rollers, conveyor belts, etc. It can also fitted with various sensors to ensure security and reliability and enables automatical connection with infrastructures for unmanned operations.
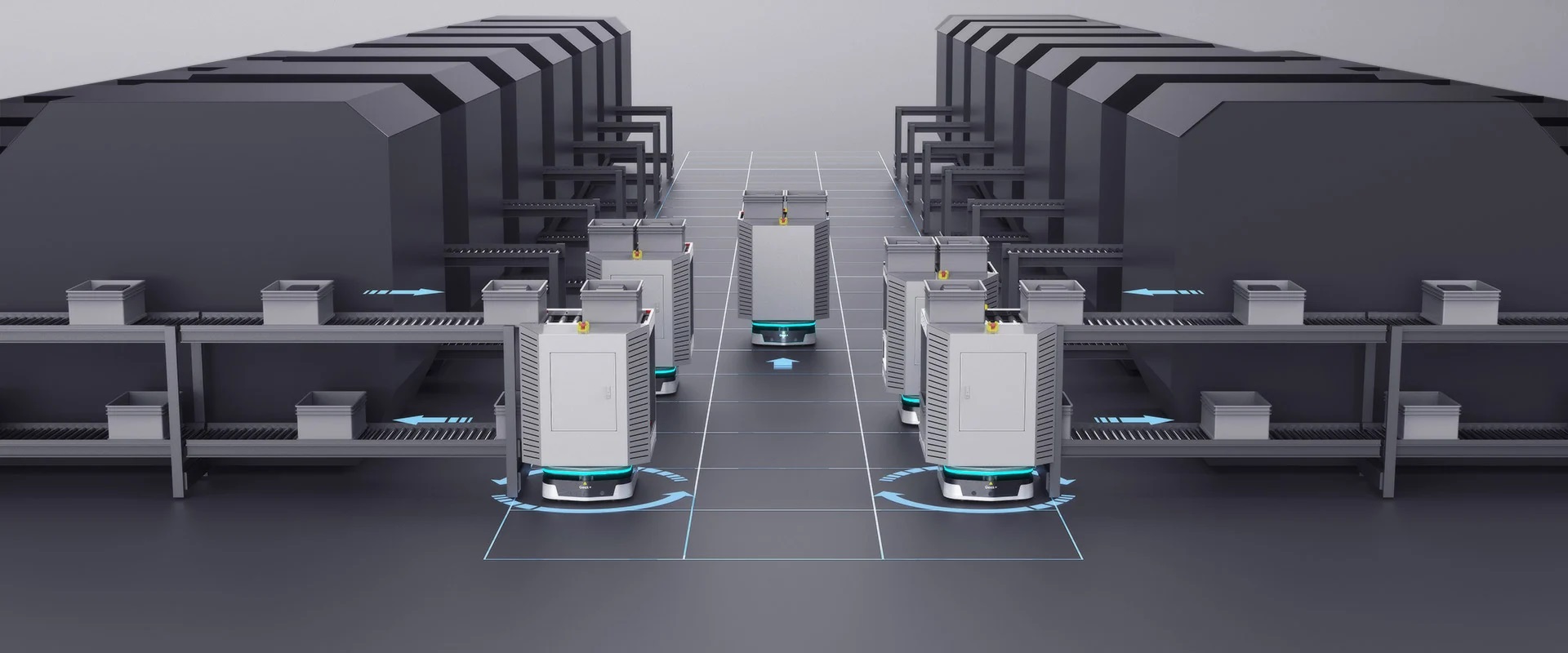
Robot Arm Hybrid
The Robot Arm Hybrid is the integration of AMR and robotic arm using Geek+ moving management system. It offers high efficiency, flexibility, and agility, replacing traditional AGV and conveyor lines to finish the last step for loading and production. It’s easy-to-deploy with ROI less than two years.
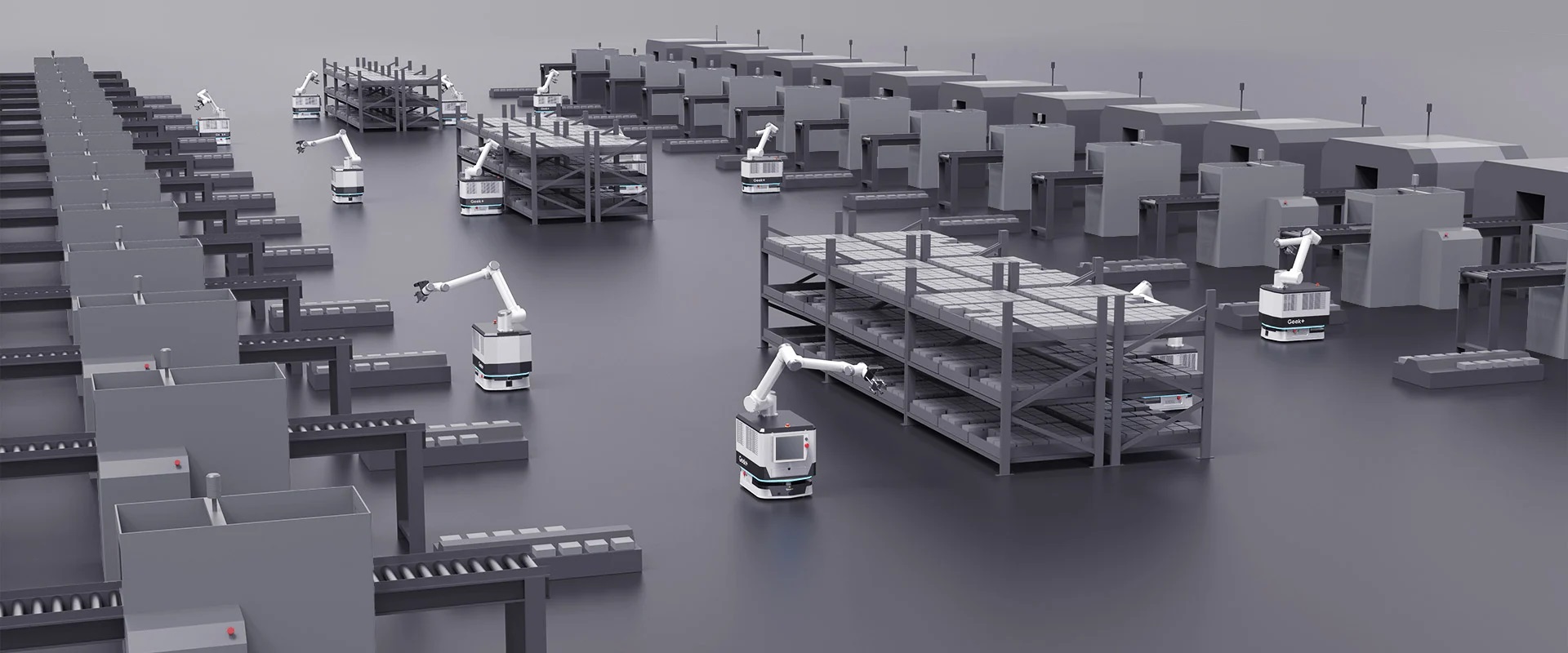
Tasks management system for logistics moving processes
Fully integrated with Geek+ robot management system, the system manages tasks, process, and scheduling of moving robots. Its robust process management capabilities can achieve optimal path planning and traffic control for hundreds of multi-type robots, It also supports cross-floor transportation. The system is user-friendly and easy to deploy.
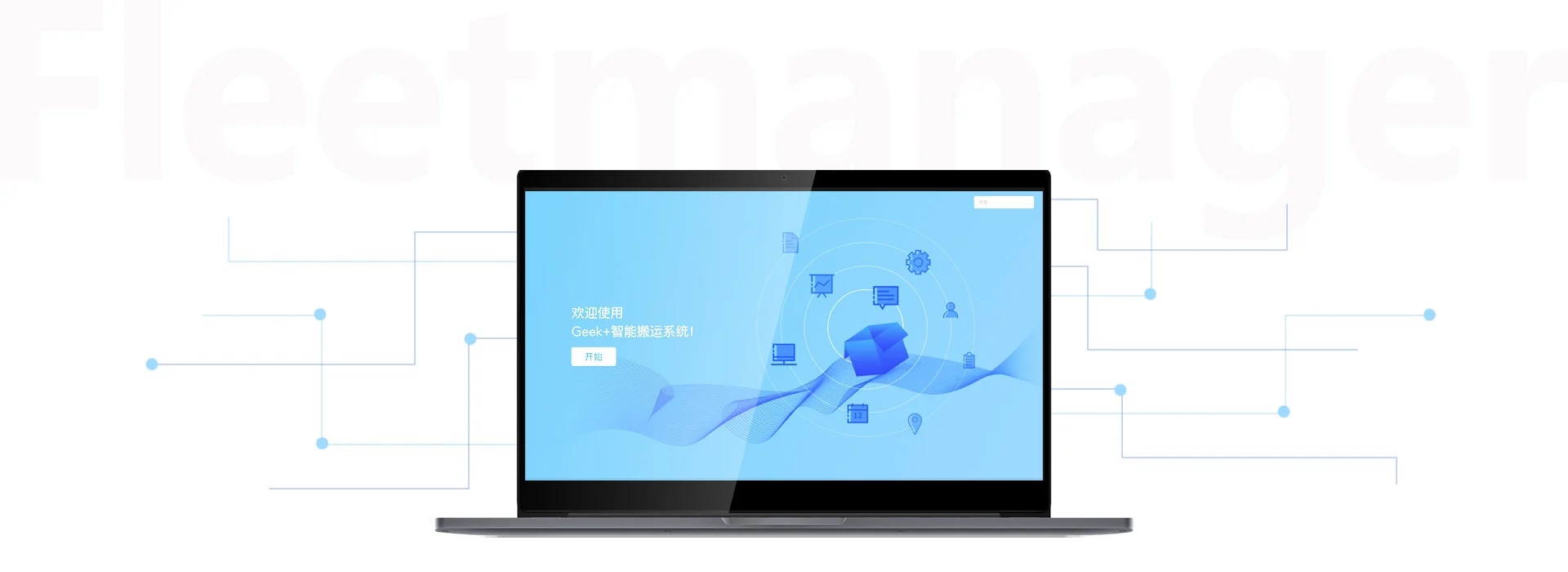
Robot management system for M series
The system provides functions of map editing and monitoring, charging station management, and log management. It can be connected with various robot modules, like rollers, traction, jacking, etc.
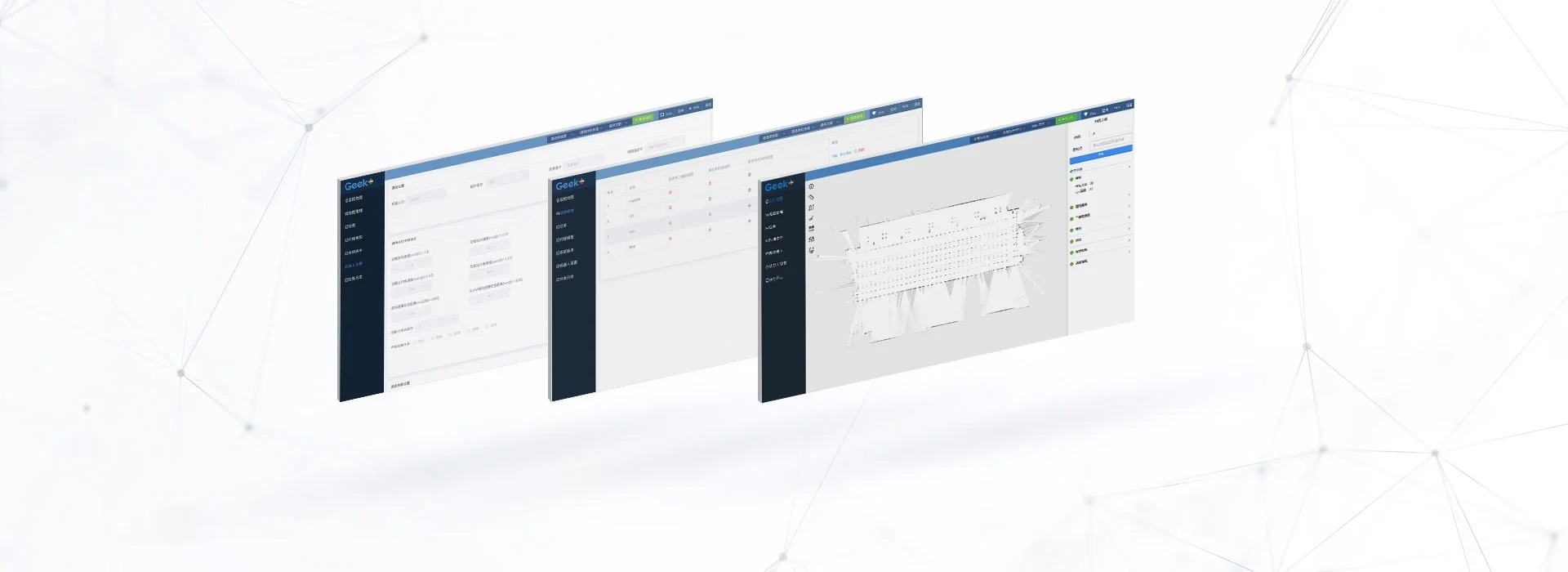
SLAM and QR code navigation
Geek+ moving robots can support both QR code navigation and SLAM navigation, switching to the most suitable one based on the working condition. SLAM navigation enables location and mapping in real-time using laser and camera sensor fusion. With SLAM, robots can maintain good positioning and motion control in a complex environment. With QR code navigation, the robot can travel fast following an accurate path.
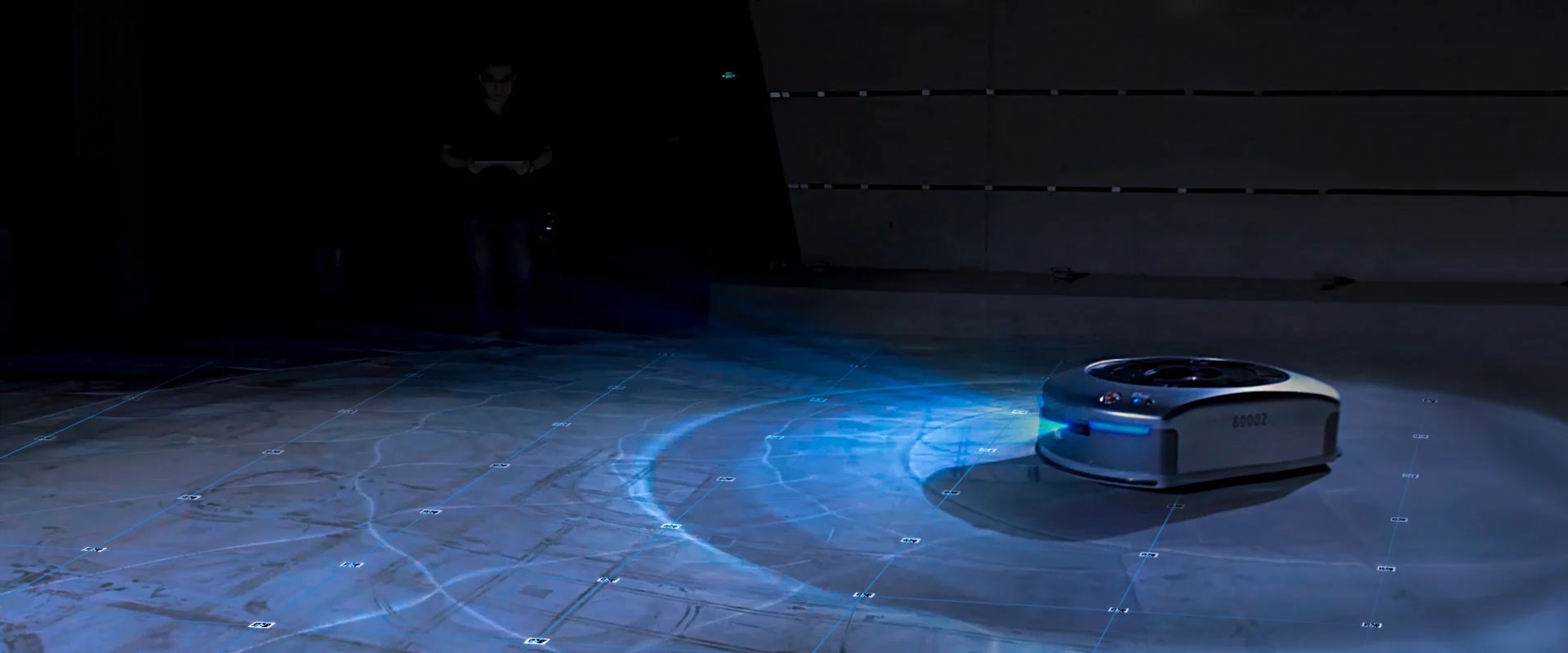
Unique advantages of moving solution
Rapid Deployment
- Ready and easy deployment for singular robots
- Short project implementation cycle of only 2-4 weeks for multiple robots
Smooth Operations
- Able to independently create and modify mapping according to requirements
- Customizable process management and charging policies
High Investment Value
- Increase in moving efficiency by at least 50%
- Possible to achieve return on investment within a year
Flexible Scheduling
- Flexible addition or removal of robots to fit changing needs
- Supports the simultaneous utilization of different models of robots
Highly Adaptable
- No need for environment modifications
- Suitable for complex human-robot interaction scenarios
Covering full moving scenarios
Geek+ Moving System is suitable for moving scenarios in warehouses of e-commerce, retail, third-party logistics, automobile manufacturing and many other industries. The four solutions have their own characteristics, covering full scene:
Lift
Warehouse pallet transport warehouse Bin or Shelf delivery of material to production lines Equipment and product moving in factory
Tugger
Cage moving warehousing logistics Shelves moving in production lines Equipment moving in factories
Bin Mover
Bin moving in warehousing logistics Shelves moving in production lines
Robot Arm Hybrid
Temporary storage warehouse picking + production line multi-station material distribution Raw material distribution + automatic line feeding Automatic inspection